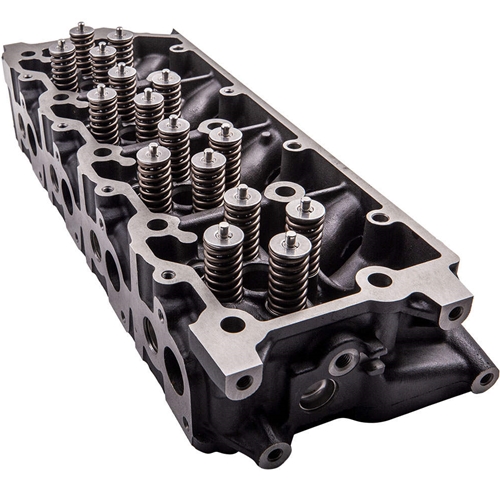
After flowing a bunch of fuel pumps on our fuel system flow bench, we started thinking that it would be interesting to see how much fuel the actual cylinder heads can move through their integral fuel rails. We started by taking some measurements, and were surprised to find that the 6.0L Powerstroke fuel rails have a smaller inside diameter than the 7.3L Powerstroke fuel rails, even though the 6.0L is rated for more HP from the factory. The 6.0L rails do benefit from the use of external supply tubes with banjo bolts, which flow more compared to the internal 1/8" NPT passages in the 7.3L heads. Still, excluding the vertical passages in the 7.3L and the external tubes in the 6.0L, the 7.3L rail volume is about 20% larger, due to having an ID that is about 5% larger and a length that is about 10% longer. This does, however, not seem to place any significant limitation on the flow capability of the 6.0L rail.
Our flow testing was performed with the system plumbed as it would be with a traditional Regulated Return setup, with the fuel entering one end of the head and exiting the other. This flow rate was measured AFTER the cylinder head, so the flow rate accounts for any restrictions created by the heads themselves, and the fittings and lines used to connect to them. The testing was done at 65psi of fuel pressure, managed after the fuel rail, just as it would be in an actual vehicle. Much like our pump flow data, we are not going to publish the numbers, but the conclusions and summary comments below should be enough to benefit anyone making fuel system choices for different power levels.
GENERAL CONCLUSIONS
- Using the precise measurements of the fuel rail volume as well as the known maximum fuel usage of each size injector, we were able to calculate how long it will take each different size injector to consume all of the fuel in the fuel rail at WOT. We then compared that data to the rate at which each different fuel pump (GPH at 65psi) could fill the fuel rail, and we were able to confirm that our fuel pump recommendations (as shown in the last article) for each size injector were valid. In a nutshell, the larger the injector, the shorter the time it takes to empty the rail. This results in needing a larger pump, which will have a shorter time to refill the rail. Ideally, you want the pump to be able to fill the rail in a measurably shorter time than the injectors can empty it in order to maintain positive fuel pressure.
- Both the 7.3L and the 6.0L heads, plumbed with typical DRIVEN DIESEL fittings/tubes/banjos, flowing in one end and out the other, are capable of supporting the largest fuel injectors available on the market (455cc for 7.3L, 500cc for 6.0L). See my COMPETITION VEHICLES note below if you will be running huge injectors in competition situations.
- As an extreme test, were able to flow over 100gph through a single 7.3L or 6.0L head using our typical DRIVEN DIESEL fittings and tubes, but we don't recommend doing this, ESPECIALLY if you don't need this much volume. Forcing diesel fuel through the rails at this kind of extremely high flow rate increase pressure drop and turbulence and will likely cause a release of air in the fuel that could even affect how the engine performs.
- We did flow both the 7.3L and 6.0L heads using Straight AN fittings (in place of the banjo bolts) in the ends of the heads, and as expected, we did see a reduction in pressure drop across the head (particularly at extremely high flow rates). Unfortunately, for street driven trucks where items like accessory drive bracketry are in the way, this kind of plumbing frequently isn't possible (nor is it necessary with all but competition level injectors and huge fuel pumps).
- COMPETITION VEHICLES (7.3L or 6.0L) running injectors at 400cc or larger and high RPM can benefit from some configuration changes. If the packaging in the race vehicle will allow, running Straight AN fittings with smooth 90° hose ends in the ends of each cylinder head (in place of the banjo bolts) can decrease pressure drop and turbulence while maintaining the benefits of a traditional regulated return. 90° elbow fittings are available for the ends of the 6.0L heads, but they are less ideal than a Straight AN fitting with a 90° hose end because the elbow will have a sharp turn that creates pressure drop and turbulence, the smooth 90° hose end does not. These vehicles are also good candidates for using the 4-Corner Feed layout in place of the traditional Regulated Return. Since they generally are not running for long periods or towing, giving up the "Flow Through" benefits of the Regulated Return for more fuel flow at the injectors may be a worthwhile trade. A combination of both the Straight AN fittings and 4-Corner Feed layout would deliver the most fuel possible for a huge injector/high RPM race build, but combinations requiring this level of fueling are realistically few and far between.
Much like Fuel Pumps, "BIGGER IS NOT ALWAYS BETTER" when it comes to how much fuel you push through the fuel rails of a 7.3L or 6.0L Powerstroke Diesel. Ideally, you want a pump configuration that is properly matched to your injectors and how the truck is used, so that you are not flowing TONS more fuel than is necessary through any part of the system. Regardless of whether it is the cylinder head fuel rails or hose/fittings elsewhere in the fuel system, too much flow rate across fittings or around sharp corners can cause pressure drop, turbulence and air release. It is clear from the testing of the cylinder heads that there is a lot of power that can be made (very large injectors can be supported) without modifications to the heads, and while maintaining the desired benefits of a traditional Regulated Return flow path. It is also clear that there are extreme power combinations running higher than normal engine RPM that would benefit from a change of configuration to ensure the maximum amount of fuel to the injectors. We suggest making your fuel system choices based on a combination of flow requirements (dictated by your fuel injectors), vehicle use (daily driving and towing are very different than short distance competition) and the pros/cons of each different fuel system design that YOU find important.
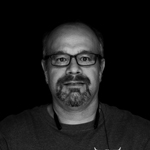
Author: Dennis Schroeder - Co-Owner of Strictly Diesel
Dennis has been Designing, Building and Supporting Aftermarket Fuel Systems for 7.3L and 6.0L Powerstrokes since 2001.