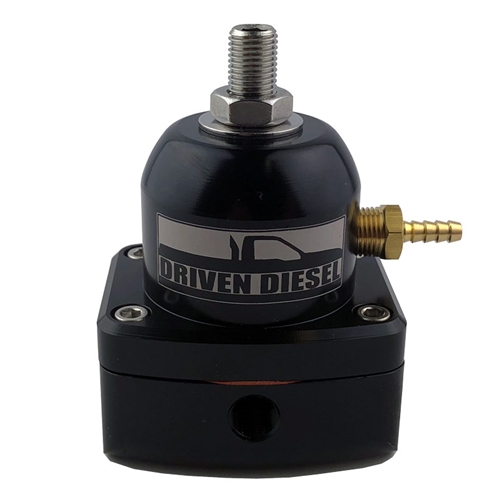
Since this article is quite long and contains a bunch of "History" that some of you may not be interested in, I did put a "Summary/Comparison" link at the bottom that will take you to a more technical "Just The Facts" discussion of the various fuel system designs.
Before I get into the discussion about the different configurations, I want to emphasize a point that I started to make in the previous article. I pointed out the fact that the 94-97 OEM fuel system is a REGULATED RETURN, and that the 99-03 OEM fuel system is a REGULATED SUPPLY. I make this distinction based entirely on the placement of the fuel pressure regulator in the system, and whether it is regulating the pressure BEFORE the fuel rails/injectors, or AFTER. I consider this to be an important distinction because the fuel pressure at different points in the system will vary, depending on where you take your measurement. Fuel pressure will drop going across a filter media, and the amount of that drop will differ based on how dirty the filter is. Pressure will drop passing through restrictive fittings, or traveling through a fuel rail with hungry injectors that are acting like "drains" on the system when they fire. Even the friction between the fuel and the hose it travels through can create pressure drop in a system, if the distance is long enough, the hose restrictive enough or the bends tight enough or frequent. As such, I personally favor designs that place the fuel pressure regulator AFTER every bit of pressure drop, and after every bit of "Demand" (the term I use to represent the variable usage of fuel from the rails by the injectors under different driving conditions).
As I get into the discussions of different designs and the testing we performed over 20 years ago, I want to be clear that the "we" I'm referring to is primarily myself and Bruce Bergdahl. Bruce was the owner of JNB Systems, and he and I co-designed the first generation of fuel system kits that I offered for sale back then. Bruce was a full time Utah fire fighter, and his workload eventually got the best of him and I bought out his interest and rebranded the product...and the rest is history. I also want to be clear about the fact that Bruce and I were not doing this in a vacuum, there were a bunch of people online trying similar modifications and posting about them. Some of what we tested was based on our own ideas, some was based on discussions with other people and attempts to validate their findings. What I'm writing about here is the work that Bruce and I did, and the results that we found, and how it led to the products we see offered today. There were other members of that community that made significant contributions as well, I mentioned some of them in the intro article, some others will get mentioned in other articles as appropriate.
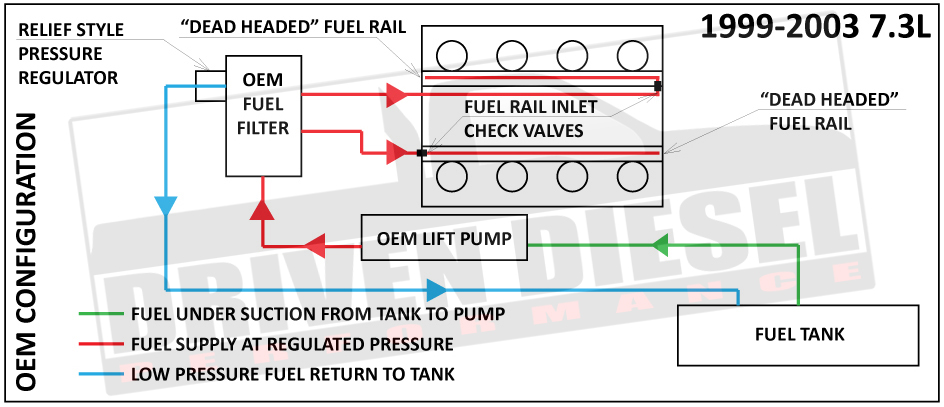
I've put the diagram of the 99-03 OEM fuel system above as a reminder of where we are starting from. These trucks had new injectors, a new electric fuel pump and a different fuel system layout than the previous generation of trucks, and many came with that darn "Cackle" that we so badly wanted to solve. The offending cylinder was #8 (lower right in this diagram, closest to the driver of the truck). If you look closely at the diagram, you will see that #8 is the last cylinder to receive fuel at the end of the dead headed fuel rail. Was there a flow issue that was resulting in this cylinder receiving inadequate fuel volume? Was air gathering at the end of the fuel rail? Was there some sort of harmonic from the fuel injectors affecting this cylinder? It's a shame I can't provide links to the old discussions that have unfortunately been lost, they were as entertaining as they were interesting.
One of the early designs I remember testing was a simple fuel rail crossover, nothing more than a hose connecting the end of each cylinder head fuel rail together, providing a path in which fuel could potentially move either direction as needed. You can see what this looks like in the diagram below, the crossover is represented in orange. Technically speaking, all this did was extend the length of each fuel rail, moving the "end point" of the rails to somewhere in the middle of the crossover, based on which side of the engine was experiencing more pressure drop at the particular moment. Since the system was still closed, there was no change in system flow or pressure with this modification.
We later incorporated an orifice into the fuel crossover fitting at the end of each rail. I remember making custom thread in orifice fittings that were screwed into the bottom of a tapped adapter fitting (those were small taps and drill bits!). This allowed us to place a T-Fitting in the middle of the crossover hose, and connect the 3rd leg of the T to the return line going back to the fuel tank. The orifice fittings limited the amount of fuel leaving the fuel rail, which was important because of the unregulated connection to the fuel return to the tank. This configuration allowed a small amount of fuel to exit the end of each rail through the orifice fitting, eliminating the "dead head" and providing a place for air to escape the rail. It also represented a new drain on the fuel supply, after the fuel pressure regulator, technically robbing some volume of fuel from the rails because the orifice sizes were fixed and always flowing. I vaguely remember feeling like this had made a difference, but that we also felt we could do better.
Both of the above Fuel Rail Crossover configurations maintained the use of the OEM fuel pressure regulator on the side of the filter bowl, making both designs a REGULATED SUPPLY type system. Even with regulator spring modifications (BBs, shims, stretching springs, replacement springs, replacement housing, etc), the OEM regulator has proven to be inadequate at best if constant/reliable fuel pressure is desired.
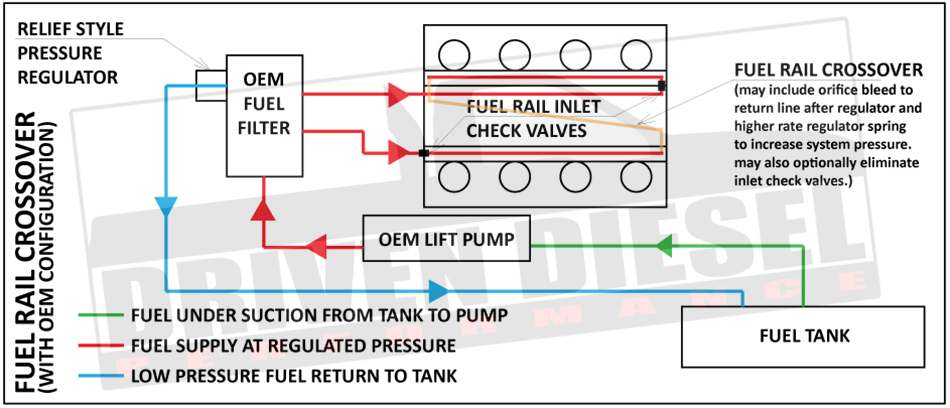
If I remember correctly, our next goal was to remove the orifices from the fittings at the exit end of the fuel rails, allowing for full fuel flow "Through" the heads, a layout more similar to the OEM 94-97 7.3L engines. Since the OEM fuel pressure regulator was integrated into the filter bowl, we had to use a plug to cap/disable it, and then an aftermarket fuel pressure regulator was installed in the middle of the fuel rail crossover line. This configuration yielded a more noticeable reduction in engine noise, as well as noticeable improvements in throttle response, and would become our First Generation REGULATED RETURN fuel system kit, which still flowed through the OEM feed lines and check valves, in the OEM direction. Wanting even more improvement, we then added replacement fuel feed lines (from the filter bowl to the cylinder heads) that eliminated the OEM check valves and increased flow, and we developed our Billet Return Fitting that replaced the regulator cap and goofy return line adapter fittings (resulting in the release of our Second Generation REGULATED RETURN fuel system kit). The new Billet Return Fitting kept the OEM return line cleanly connected to the filter bowl, maintained the OEM air bleed from the filter bowl (handy when changing filters) and provided a much cleaner connection point for the fuel return from the fuel pressure regulator.
Over the years, the return fitting has been made more robust (the first generation fitting experienced some failures due to the assembly method used) and the system as a whole has been updated with more CNC bent S.S. tube sections and higher quality hose assemblies (somewhat dictated by the use of Ultra Low Sulfur Diesel, Bio-Diesel and various fuel additives), as well as S.S. brackets. We also now feed both heads at the front and return from the rear (an attempt to limit additional heatsoak of the fuel supply from hot exhaust/turbocharger components). See the diagram of our current "Standard" Regulated Return kit below.
NOTE: I'm not going to cover the "Fuel Bowl Delete Regulated Return" separately at this point, except to say that it came about several years after the research described above, based on a request from Jody Tipton at DP-Tuner, at a time when 7.3L "Performance" was really starting to grow. More details on the FBD setup later.
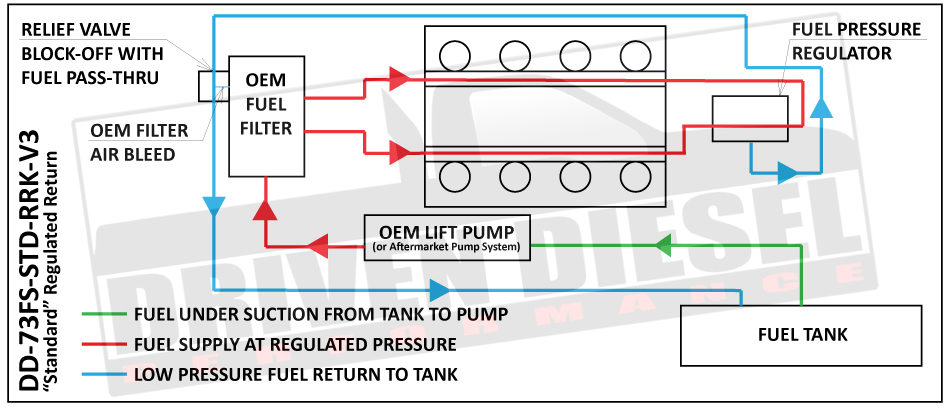
Another engine fuel system configuration we tested while chasing Cackle was the "Single Circuit Regulated Return". Like the dual circuit version, this design doesn't allow air to be trapped in the rails and it moves the fuel pressure regulator (aftermarket) to after the rails (making it a true REGULATED RETURN). This layout didn't provide any noticeable benefits or changes when compared to the dual circuit layout, but we did feel like there could be a few drawbacks so we stuck with the dual circuit design. See the diagram of a Single Circuit Regulated Return below.
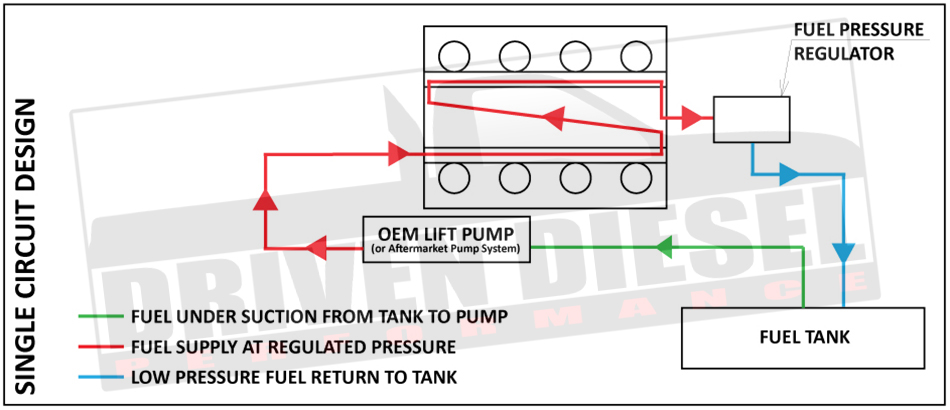
While working on these articles, I was going through my old computer files for the early fuel system kits to see what I still had. I was pretty excited to find that I still have these original drawings that Bruce did as we were going through our testing of each of these system configurations. Thought it might be cool to share them here.
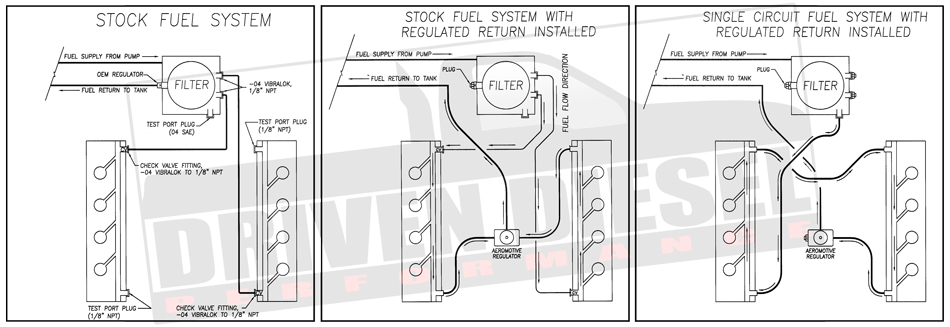
The above testing went on over a pretty lengthy period of time, maybe longer than a year. We were making changes, driving the trucks to see what (if anything) we accomplished, then making more changes. At the same time, there were other parts of the fuel system getting attention as well, but that discussion is for another article.
I mentioned at the top of this article that I would provide a link to a Summary/Comparison Article. This article will offer a more technical comparison of the fuel system designs discussed above, as well as one last configuration that has become popular more recently. CLICK HERE.
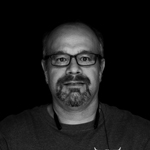
Author: Dennis Schroeder - Co-Owner of Strictly Diesel
Dennis has been Designing, Building and Supporting Aftermarket Fuel Systems for 7.3L and 6.0L Powerstrokes since 2001.