
Common Pressure Side Leaks
NPT / Pipe Thread Fittings : Pipe thread fittings are probably the single largest cause of leaks in any modified fuel system. These fittings use tapered threads that fit tighter and tighter to each other as the fitting is tightened. Pipe thread fittings require the use of some type of thread sealant (Teflon tape, pipe dope, Loctite 545, etc) to prevent leaks. The seal ends up being a combination of the chosen thread sealant, and the tightness of the tapered threads after installation. Unfortunately, there are three common causes of leaks with pipe thread fittings.
The first cause is "sealant related". This can be "lack of sealant" (either none used, or not enough used) or improper application of the sealant. If you are using Teflon tape, we recommend 2-3 wraps in a clockwise direction (threads facing you) so that the tape doesn't bunch up when installing the fitting. If you are using a liquid sealant, we recommend using enough sealant to cover at least 3/4 of the threads, and making sure the sealant is equally applied all the way around the fitting. With liquid sealant, we also recommend allowing the sealant to cure after installation of the fitting before putting pressure to it.
The second cause is under tightening the pipe thread fitting. Because pipe thread sealing is a function of the threads getting tight to each other, if the fitting is left too loose, there will be a gap between the threads that allows for a leak. If you are installing a straight fitting, simply apply the sealant of your choice, install the fitting and tighten until you feel significant resistance. Keep in mind that if you do have a small leak, you can always tighten it a tad more if needed. If you are dealing with a 45° or 90° fitting, you generally need the fitting to stop while pointing in a particular direction...and it isn't always where the threads tighten up (you can almost count on just the opposite). If you are using a good liquid sealant, and the threads are pretty close to tight when you get the fitting where you need it, you can try just letting the sealant fully cure before putting fuel pressure to it. If the fitting is too loose when oriented correctly, but you can't get another full turn because it gets too tight when pointing the wrong direction, you may need to switch to Teflon tape. When installing angled fittings, Teflon tape alters the thickness of the threads on the fitting and changes the point where the fitting gets tight. If the fitting doesn't get tight soon enough, you can clean off the tape and add another wrap of tape so it tightens up sooner. If you need it to turn farther, you can use a bit less tape. The goal is to use just the right amount of tape so your angled fitting gets tight where you need it to.
The third and worst cause of leaks with pipe thread fittings is over tightening, which can lead to cracking the female port. Thankfully this is not a very common problem, but it is one you need to be aware of and it is the reason we mention being careful when installing pipe thread in our instructions. While the fitting being tight is important to getting the threads to seal, that does NOT mean that you should slip into your favorite super hero underoos and get out the 6' breaker bar or 1/2" impact. There is an aspect of "feel" to pipe thread fittings. They should be installed with hand tools, and if it feels tight, it probably is. Better to stop slightly short and have to put a tiny bit more rotation on it to get it to seal, or have to pull it and reseal it, than to go too far and damage the receiving port. Like any fastener, if you are tightening and it suddenly gets loose again, it is time for a break and an adult beverage!
O-Ring Fittings : Whenever possible, we try to use o-ring fittings because they are just more reliable and easier to deal with than pipe thread. The fuel pressure regulator and fuel bowl delete block in our kits, as well as some 6.0L OEM locations, use an o-ring type fitting. Best practice is to lubricate the o-ring with diesel fuel before installation so it doesn't bind. If you have a leak at an o-ring fitting, and the fitting is tight, generally the o-ring needs to be replaced as it is either "flat" or has gotten a tear that is causing the leak. The one possible exception is the 90° elbows we supply for the factory fuel filter bowl in a 6.0L. These fittings have an o-ring with a backup washer and nut so they are adjustable. They are shipped from the manufacturer with a thinner metal ring around the outside of the o-ring. That thinner ring needs to be removed for the o-ring to seal. If you have a leak at one of the 90° fittings on a 6.0L fuel filter bowl, make sure there isn't an extra thin metal ring around the o-ring.
Thread sealant should NEVER be used on o-ring fittings.
Tube to Fitting Leak : Our CNC bent tubes will either have a male end (for connection to a female hose end) or a female end (for connection to a male fitting). In either case, the connection is a military style AN type that uses a 37° metal to metal flare to make the seal. If you have a leak where the female end of the tube is connected to a male fitting (rare), there are two possible causes. First, both sealing surfaces need to be examined for damage (crack, groove) or debris. If no debris is found, make sure the sealing surfaces are clean and undamaged and reinstall and tighten securely. There is a reinforcement sleeve under the tube nut, so you can tighten the nut quite aggressively provided you are holding the fitting with another wrench. The same goes for addressing a leak between a hose end and the male end of one of our tubes. Generally speaking, all that is needed is to clean the sealing surfaces and reinstall and tighten properly.
In cases where a tube is connecting to two fixed fittings, it is important to look at the angle that the tube meets the fitting. The female flare of the tube should meet the male cone of the fitting evenly all the way around. If the tube seems to meet the fitting in a manner that is "off to one side", something will need to be adjusted to correct the angle or a leak will be the likely result. Generally in our kits, when this is a possibility, we include washers or shims to adjust the position of one of the fixed components. It is always best to visually check the alignment of the tube to the fitting before installing the nuts and tightening.
Thread sealant should NEVER be used on 37° AN style fittings.
Leak in Teflon Hose : While it doesn't happen often, sometimes we find fuel leaking from under the protective covering of one of our hoses. This is an indication that the Teflon liner in the hose has a hole in it, allowing fuel to leak and run out of the outer covering. Our Teflon hoses are rated for over 3000psi, so these leaks are rare. Like anything else "man made", there can be a manufacturers defect in the hose, which is why we cover them for 1 year from the purchase date. The most common cause of leaks in the middle of a Teflon hose is some kind of "physical damage". The Teflon liner in the hose can only be bent so far before it kinks like a drinking straw. Crushing one of these hoses will have the same effect. Because the Teflon hose has a S.S. braided cover (under the protective covering), it is possible (though more difficult with the outer cover) to short the hose to an 12v+ source (top of the glow plug relay, back of the alternator, etc), which will cause the S.S. braid to get hot enough to damage the Teflon liner. Lastly, it is also possible to damage a Teflon hose with a strong static shock, which will cause a hole in the Teflon.
Crimped Hose End Leaking : While also rare, this would be the more common place to have a leak on one of our S.S. braided Teflon hoses. If the fuel is leaking from between the hose and the crimped fitting, either the hose or fitting had a problem before assembly, or possibly the hose wasn't inserted fully or the fitting wasn't fully crimped.
Incomplete Fitting Weld on Tube : Some of our S.S. tube assemblies have a fixed (non-movable) fitting at one or both ends. Our current quality control processes have made this much more rare, but every once in a while we have one slip through where a fitting isn't fully welded. This is generally pretty obvious as you will have fuel spraying from the joint where the tube meets the fixed fitting. If the weld issue is very small, it may just be a drip. If you closely inspect the fixed fitting and find a nice smooth weld all the way around, except for a small area that seems to have been missed, that is likely the source of the leak. We cover this under our warranty and will send out a replacement if necessary.
Failed Regulator Diaphragm : If you have fuel coming out of the "boost reference port" on your regulator (nipple on the top half of the regulator), the diaphragm has a hole in it. This happens from time to time, as the diaphragm is flexible and cycles in response to fuel pressure changes as well as pulses in the fuel system that are created by the operation of the injectors. We stock replacement diaphragms for Fuelab regulators. Refer to my previous article (Stop Blaming The Regulator) for information about taking the regulator apart to replace the diaphragm.
Spin-On Fuel Filter Leak : Occasionally we have a customer with a persistent leak between the spin-on fuel filter and the fuel filter head we supplied in our kit. If you run into this, and replacing the filter doesn't solve the problem, you may need to remove the filter head to more closely examine it. From time to time we have seen the nipple that the filter screws onto installed at an angle. When you screw the filter on, one side of the gasket would contact the sealing surface, and the opposite side (180° around from where the gasket is touching) would still have a large gap. Even though you could tighten the filter enough for the gasket to touch all the way around, it wasn't enough to stop leaking. Sadly, we had the most problem with this when using the shiny filter heads that are made in the US, which is why we went back to the foreign units. Because of the angle of the threads, it is not uncommon for there to be a small gap, which is easily sealed when the filter is fully tightened (the gasket offers a lot of "crush").
Also, there have been instances where a customer thought the leak was coming from the filter to filter head seal, but it ended up being a cracked filter head from overtightening one of the pipe thread fittings or plugs. When the leak is at the filter head, it is not always easy to see where it is coming from when installed in the vehicle.
Still Lots Of Other Possibilities : Depending on the truck, which stock components are still in use and which aftermarket products are installed, there may be other possible types of leaks in the system. There are some fittings (like banjo bolts) that seal with a replaceable copper washer. OEM 7.3L banjo bolts seal with an o-ring. You can have leaks at the o-ring between the OEM fuel filter lid and fuel filter canister, leaks at the o-rings that seal the water drain on the OEM 7.3L fuel bowl, etc. Any leak needs to be closely examined to see where it is coming from and why it is leaking in order to know what to do to repair it. I tried to cover the most common leaks that come with running an aftermarket fuel system above. Almost anything else should be relatively easy to figure out.
Hopefully your fuel system connections are now as dry as this article. Next up...some other issues we see on the pressure side of the fuel system.
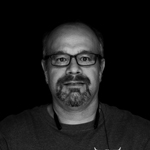
Author: Dennis Schroeder - Co-Owner of Strictly Diesel
Dennis has been Designing, Building and Supporting Aftermarket Fuel Systems for 7.3L and 6.0L Powerstrokes since 2001.