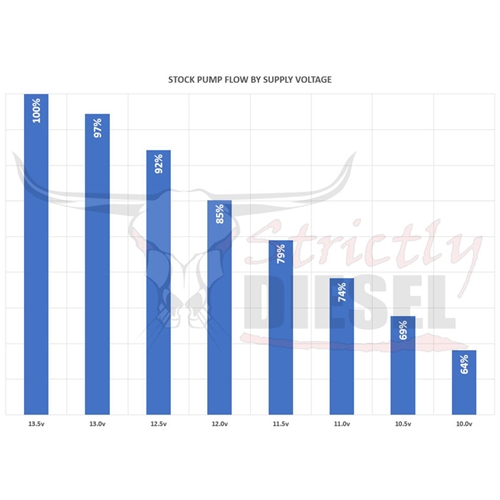
If you read my first fuel system article (Stop Blaming The Regulator!), you know that most customers immediately assume that the fuel pressure regulator, or the Regulated Return fuel system kit, are to blame for their low fuel pressure woes. Once we explain the situation and confirm that the regulator isn't the source of their problem, we can move on to actually diagnosing the truck and finding the real culprit. It may be old, but the KISS Principle (keep it simple stupid) still applies, so the best place to start is with the basics. Having learned in the previous article that "pressure requires flow", it is generally safe to assume that if you have low fuel pressure (with a working regulator), you have low fuel flow (this is not a guarantee, but a good place to start). Since the fuel pump (commonly referred to as a lift pump) is what provides the fuel flow, it becomes the next logical place to look.
A Quick And Easy Test
NOTE: The following assumes that your fuel pump is running, and so is the truck, you just have a low fuel pressure concern (either all the time, or under load). If the pump is not running, you can still use the information below to help track down the problem, just know that you are likely dealing with a dead pump or no power at the pump due to a blown fuse, bad wiring or something like that.
Before we get into the more involved diagnostic steps (which will be covered in a different article), we need to make sure that we appear to have a working lift pump. Whether we are dealing with a bone stock OEM pump, dual OEM pumps, or any one of the other pump setups on the market, the following is still applicable. Don't skip this test, it could save you a ton of time!
1. Using a good Voltmeter, check your battery voltage at the batteries, ideally with the engine running for about a minute so that the glow plugs have turned off and the alternator is charging. You should have around 13.5v. If you don't, you need to have your batteries and alternator checked before proceeding. Seriously, don't try to chase possible electrical issues if the batteries and charging system aren't working correctly.
2. Now, check the voltage right at your fuel pump under the same conditions. Some pumps have screw terminals you can easily touch the leads to, some you will need to carefully pierce the wires with the tips of the voltmeter leads. Either way, what you want to see is the SAME VOLTAGE at the pump that you have at the batteries. If the voltage at the pump is significantly lower than the voltage at the batteries, you've got an electrical problem that needs to be tracked down.
To understand why this is a problem, look at the chart below. This is actual data from our fuel pump flow bench, based on a single OEM 7.3L Bosch pump (different pumps will vary). If your charging system isn't working and your pump is running at only 12.0v, you've lost 15% of the flow from the pump. If you've got electrical issues and the pump is only seeing 10.0v, you've lost 36%. Simply put, lower input voltage means lower flow, which can turn into lower pressure under the right conditions.
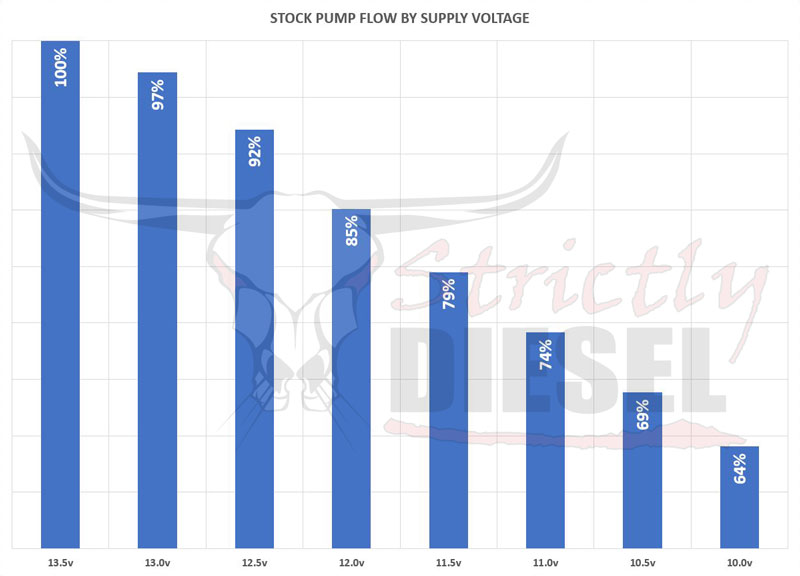
If you think this type of issue isn't likely, consider the fact that my most recent motivation for writing this article was trying to help someone on Facebook that had already replaced both pumps in his dual setup (~$250) and was planning to replace the regulator (~$150) next. I asked him early on about how the pumps were wired and what the voltage was, but never got a reply. Over a week later, after asking again, he finally discovered that he only had 9.5v at the pumps. This truck would start and run just fine, but with his larger aftermarket injectors (and dual stock pumps to support them), he was seeing pressure drop under throttle that was bad enough to cause a loss of power. At only 9.5v his dual pump setup was barely exceeding what a good stock single pump can flow, and that wasn't enough to keep his hungry aftermarket injectors fed. Even worse, he had already spent about $250 on parts that had not fixed the problem, and was prepared to spend another $150 throwing more unnecessary parts at it...and that isn't an outcome that anyone wants.
Though we have not done low voltage testing of other fuel pumps, we would expect fuel flow to drop off as voltage falls from almost every electric fuel pump that is commonly used in 7.3L and 6.0L applications. The biggest exception would be the Fuelab Prodigy pumps, because they have an internal speed controller and are designed to operate consistently within a range of 12.0-16.0v (but may fail to start with voltage significantly below 12.0v).
Why Is My Voltage Low?
The answer to this question can take some investigating. It will depend on whether your setup is still using OEM wiring, or if you have upgraded to an aftermarket harness that includes larger wire and a relay. It could be a damaged wire, an undersized wire, a faulty connector, a bad ground, a bad relay, a loose connection...or some combination of more than one of those. There is no easy way to cover every possibility, but here are some recommendations and suggestions that should help.
Perform a thorough visual inspection of all of the wiring you can see. Check any connectors for signs of wires pulling out or being broken or frayed. Check connector pins for damage and make sure they are locked into the connector and don't push out. Inspect any exposed wires for signs of the insulation being melted or damaged. If there is a relay, pull it out of its socket and inspect the relay and socket pins for looseness or signs of arcing (burn spots).
If there is a fuse, you can visually inspect it, but a better bet is to probe the voltage by piercing the wire before and then after the fuse and its holder and comparing the readings. If the voltage is lower after the fuse, it may be partially blown, replace it and check voltage again. If the voltage is still lower, the fuse holder may need to be cut out and replaced.
Should you need to modify or replace your fuel pump wiring, either to fix a problem or support an aftermarket pump, here are some things to consider:
• OEM wiring is for the OEM pump. If you upgrade the pump, upgrade the wiring.
• Running 2 OEM pumps on the OEM wiring is NOT a good idea!
• Old trucks have old wiring and components and they don't last forever!
• Most aftermarket pumps will do great with 12ga wiring on a 30A relay.
• Really large aftermarket pumps may require 10ga wiring on a 40A relay
• When it comes to electrical, the cheap way is almost always the wrong way!
For those of you that don't have the knowledge or desire to build your own fuel pump wiring harness, we can certainly help you with that:
• 94-97 7.3L Trucks with Electric Fuel System Conversions CLICK HERE
• 99-07 7.3L and 6.0L Trucks/Excursions CLICK HERE
If you found a low voltage situation while following the test procedure above, fixing it is likely to take care of your fuel pressure problem. If you didn't, at least you know at this point that you have correct voltage at the pump, and the pump is running. This doesn't mean the pump is working correctly, but we can now move on to other diagnostic methods to determine the cause of the low pressure condition.
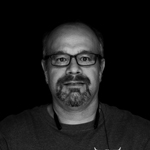
Author: Dennis Schroeder - Co-Owner of Strictly Diesel
Dennis has been Designing, Building and Supporting Aftermarket Fuel Systems for 7.3L and 6.0L Powerstrokes since 2001.